Our Products
Trust the Experience

Vertical Band Sealer Machine
The Vertical Band Sealer Machine is a versatile packaging equipment designed to efficiently seal bags of various sizes in a vertical orientation. It utilizes a heated sealing band to create strong and reliable seals on a wide range of materials such as polyethylene, polypropylene, laminates, and other heat-sealable films. This machine is ideal for industries requiring high-speed, continuous sealing of bags to ensure product freshness and integrity.
- For all Sealing Purposes
- Food Industry: Used for sealing bags of snacks, grains, confectionery, and frozen foods.
- Pharmaceuticals: Seals medication pouches and packages.
- Cosmetics: Seals bags containing powders, creams, and other beauty products.
- Chemicals: Seals bags for fertilizers, detergents, and other chemical products.
- Electronics: Used for sealing bags containing electronic components to protect from moisture and contaminants.
- Textiles: Seals bags for garments, fabrics, and textiles during shipping and storage.
- Efficiency: High-speed sealing for increased productivity.
- Versatility: Can seal a variety of bag sizes and materials.
- Consistency: Creates uniform and reliable seals.
- Preservation: Seals in freshness and protects products from external elements.
- Cost-Effective: Reduces manual labor and ensures efficient packaging processes.
- Sealing Band: The machine features a heated sealing band that can reach temperatures necessary for effective sealing of various materials. The temperature is adjustable to accommodate different film types.
- Conveyor System: A conveyor system moves the bags vertically through the sealing process, ensuring consistent seals and efficient operation.
- Adjustable Height: The machine is often equipped with an adjustable height feature, allowing it to accommodate different bag sizes.
- Digital Controls: Many models come with digital controls for easy operation and precise adjustment of settings such as sealing temperature and conveyor speed.
- Sealing Pressure: The machine applies uniform sealing pressure to ensure strong and airtight seals.
- Cooling System: Some models include a cooling system to quickly solidify the seal after it’s made, reducing the time needed between sealing cycles.
- Safety Features: These machines often have safety features such as emergency stop buttons and protective guards to ensure safe operation.
Regular maintenance of the Vertical Band Sealer Machine is essential for optimal performance and longevity. This includes:
- Cleaning: Regularly clean the sealing band and conveyor system to prevent buildup that could affect sealing quality.
- Lubrication: Keep moving parts properly lubricated to reduce wear and ensure smooth operation.
- Inspection: Periodically inspect components such as the sealing band, conveyor belt, and electrical connections for signs of wear or damage.
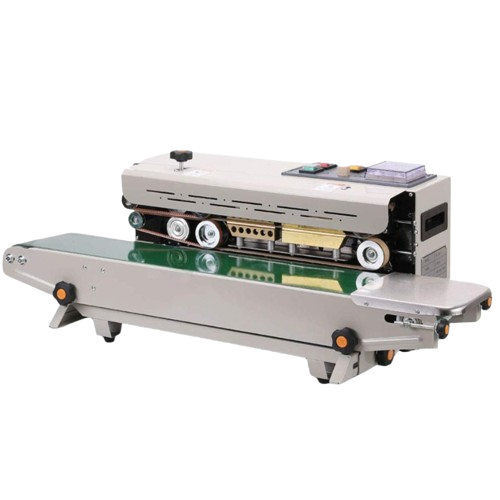
Horizontal Band Sealer Machine
The Horizontal Band Sealer Machine is a versatile and efficient packaging solution designed for sealing a wide range of bags horizontally. It utilizes a continuous band sealing mechanism to create secure, airtight seals on bags, ensuring product freshness and integrity. This machine is widely used in various industries such as food, pharmaceuticals, cosmetics, and more, where consistent and reliable sealing is essential.
- For all Sealing Purposes
- Food Industry: Ideal for sealing snack bags, bakery products, frozen foods, and more.
- Pharmaceuticals: Ensures airtight seals for medication packets, test kits, and medical supplies.
- Cosmetics: Perfect for sealing pouches containing creams, lotions, and beauty products.
- Industrial Products: Seals bags containing hardware, electronics, parts, and other industrial goods.
- Efficiency: High-speed sealing, improving production rates.
- Consistency: Ensures uniform and secure seals for product freshness.
- Versatility: Can handle a variety of bag materials such as polyethylene, polypropylene, laminates, and more.
- Ease of Use: Simple controls and adjustments for different bag sizes.
- Cost-Effective: Reduces the need for manual sealing, saving labor costs.
- Quality Seals: Ensures tamper-evident and leak-proof packaging.
- Sealing Mechanism: Continuous horizontal band sealing.
- Sealing Width: Adjustable, typically ranging from 8mm to 15mm.
- Sealing Speed: Variable speed control, ranging from 0 to 12 meters per minute.
- Power Requirements: Typically operates on standard 110V or 220V power supply.
- Construction: Stainless steel or sturdy metal frame for durability.
- Conveyor Belt: Allows for easy feeding of bags for continuous sealing.
- Temperature Control: Adjustable temperature settings for different bag materials.
Proper maintenance ensures the optimal performance and longevity of the Horizontal Band Sealer Machine. Here are some maintenance tips:
- Regular Cleaning: Wipe down the machine after each use to remove dust, debris, and spilled product.
- Lubrication: Apply lubricant to moving parts and conveyor belts to prevent friction and wear.
- Check Sealing Elements: Inspect the sealing elements regularly for wear or damage. Replace as needed.
- Temperature Calibration: Periodically check and calibrate the temperature settings to ensure consistent sealing.
- Belt Alignment: Ensure the conveyor belt is properly aligned to prevent jams and uneven sealing.
- Electrical Components: Keep electrical components clean and dry. Check for loose connections.
- Professional Servicing: Schedule routine professional maintenance to check for any issues and ensure optimal performance.
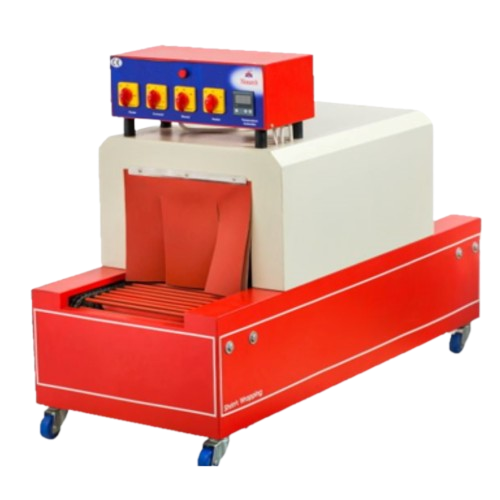
Shrink Machine
The Shrink Machine is a versatile and efficient packaging solution designed to securely wrap products in shrink film. Utilizing heat, this machine applies heat to the shrink film, causing it to shrink and conform tightly around the product, creating a protective seal. Its compact design and user-friendly interface make it ideal for a variety of industries requiring reliable packaging solutions.
- Wrapping a layer of plastic around everything which needs to be held together
- Food Industry: Perfect for packaging food items such as fresh produce, meats, and baked goods.
- Manufacturing: Ideal for packaging electronics, tools, and other manufactured goods.
- Retail: Provides a professional and secure wrapping for products on store shelves.
- Shipping & Logistics: Ensures products are securely wrapped for safe transportation.
- Pharmaceuticals: Safely seals medication bottles and other pharmaceutical products.
- Efficiency: Rapidly wraps products, saving time and increasing productivity.
- Versatility: Accommodates a wide range of product sizes and shapes.
- Cost-Effective: Reduces material waste with precise film usage.
- Professional Presentation: Enhances the appearance of products with tight, uniform wrapping.
- Protection: Shields products from dust, moisture, and tampering.
- Heat Source: Electric heating elements
- Material: Stainless steel construction for durability and hygiene
- Control Panel: Intuitive interface with temperature and speed controls
- Size: Compact design, suitable for small to medium production lines
- Power Requirements: Standard electrical outlet compatibility
To ensure optimal performance and longevity, regular maintenance of the Shrink Machine is recommended:
- Cleaning: Regularly clean the machine after use to remove any film residue.
- Inspection: Check heating elements for signs of wear or damage.
- Lubrication: Keep moving parts lubricated for smooth operation.
- Calibration: Periodically calibrate temperature and speed settings for efficiency.
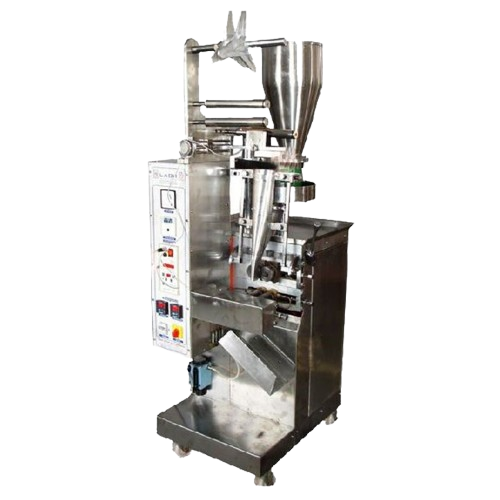
Vertical Pouch Packing Machine
The Vertical Pouch Packing Machine is a versatile and efficient packaging solution designed to package various types of products into pouches. It is widely used in industries such as food, pharmaceuticals, chemicals, and more. This machine is capable of forming, filling, and sealing pouches with precision and speed, ensuring product freshness and integrity.
- Spices, Pills, Capsules, Powders, Detergents, Pet Food, Fertilizers, Seeds, Grains, Namkeen, Napthelean Balls, Chocolates, etc.
- Food Industry: Used for packaging snacks, powders, grains, spices, sauces, and more.
- Pharmaceutical Industry: Ideal for packaging tablets, capsules, powders, and other pharmaceutical products.
- Chemical Industry: Suitable for packaging granules, powders, liquids, and other chemical products.
- Cosmetics Industry: Used for packaging creams, lotions, gels, and other cosmetic products.
- Hardware Industry: Packaging small hardware items, screws, nuts, and bolts efficiently.
- Efficiency: High-speed packaging, increasing productivity.
- Versatility: Can handle various types of products and pouch sizes.
- Precision: Accurate filling and sealing, minimizing product waste.
- Hygiene: Designed for easy cleaning and maintenance, meeting hygiene standards.
- Cost-Effective: Reduces labor costs and material wastage.
- Compact Design: Saves floor space in production facilities.
- Pouch Forming: The machine forms pouches from a roll of packaging material, which is fed through the machine.
- Product Filling: Products are accurately filled into the pouches using volumetric or weighmetric fillers.
- Sealing: Pouches are sealed using heat sealing technology, ensuring airtight and secure packaging.
- Control System: Equipped with an advanced control system for precise operation and monitoring.
- Material: Constructed with stainless steel for durability and easy cleaning.
- Power Requirements: Operates on standard electrical power supply.
- Capacity: Output capacity varies based on model, ranging from 30 to 100 pouches per minute.
Regular maintenance is crucial for the smooth operation and longevity of the Vertical Pouch Packing Machine. Here are some maintenance tasks:
- Cleaning: Regularly clean the machine after use to prevent residue buildup.
- Lubrication: Lubricate moving parts as per the manufacturer’s guidelines to prevent wear and tear.
- Inspection: Periodically inspect belts, seals, and other components for wear and replace as needed.
- Calibration: Ensure the machine is calibrated for accurate filling and sealing.
- Training: Train operators on proper use and maintenance procedures.
- Documentation: Maintain a maintenance log to track servicing and repairs.

Pneumatic Pouch Packing Machine
The Pneumatic Pouch Packing Machine is a versatile and efficient packaging solution designed to streamline the packing process for a variety of products. Utilizing pneumatic technology, this machine automates the filling and sealing of pouches, ensuring speed, accuracy, and consistency in packaging.
- Spices, Pills, Capsules, Powders, Detergents, Pet Food, Fertilizers, Seeds, Grains, Namkeen, etc.
- Food Industry: Ideal for packaging snacks, spices, grains, pulses, and other food products.
- Pharmaceuticals: Suitable for packing tablets, capsules, powders, and small medical devices.
- Cosmetics: Used for packaging creams, lotions, and gels into pouches.
- Hardware and Components: Efficiently packs small parts, fasteners, and components.
- High Efficiency: The pneumatic system ensures quick and precise operations, enhancing productivity.
- Versatility: Can handle various pouch sizes and types, adapting to different product requirements.
- Sealing Quality: Provides consistent and reliable sealing, maintaining product freshness.
- Ease of Use: User-friendly controls and adjustments make it simple to operate.
- Space-saving: Compact design saves floor space in production areas.
- Cost-effective: Reduces labor costs and minimizes material wastage.
- Hygienic: Constructed with materials suitable for food and pharmaceutical industries, ensuring cleanliness and compliance.
- Pneumatic System: Utilizes compressed air to power the machine’s operations, including filling, sealing, and cutting.
- Filling Mechanism: Can be equipped with volumetric, auger, or piston filling mechanisms depending on the product.
- Sealing Method: Typically employs heat sealing for airtight and secure pouches.
- Material: Constructed with stainless steel for durability and easy cleaning.
- Control System: PLC (Programmable Logic Controller) for precise control of operations and settings.
- Speed: Variable speed control to adjust packing speed as needed.
- Power Requirement: Runs on standard electrical power with an air compressor for the pneumatic system.
Proper maintenance ensures the longevity and optimal performance of the Pneumatic Pouch Packing Machine:
- Regular Cleaning: Remove debris, dust, and residue from the machine’s surfaces.
- Lubrication: Apply lubricant to moving parts to prevent friction and wear.
- Inspection: Periodically check for loose bolts, worn-out seals, or damaged components.
- Calibration: Ensure accurate filling and sealing by calibrating the machine as needed.
- Training: Train operators on proper use and maintenance procedures.
- Scheduled Servicing: Arrange for professional servicing at recommended intervals.
- Spare Parts: Keep essential spare parts on hand for quick replacements when necessary.
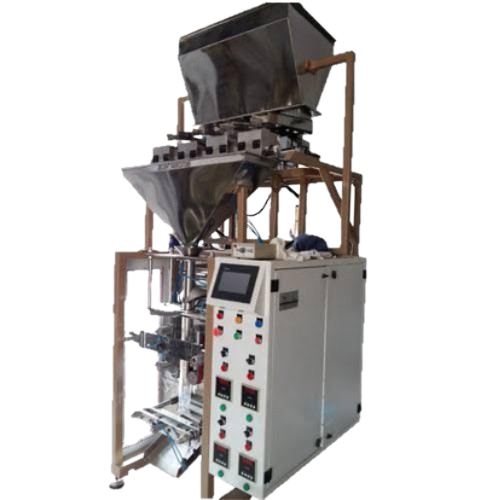
Load-Cell Weight Filler Machine
A Load-Cell Weight Filler Machine is a precision instrument designed to accurately measure and dispense products by weight. This machine utilizes load cells, which are transducers that convert force into an electrical signal. When a product is placed on the filling platform, the load cell measures the weight, allowing the machine to dispense the exact desired amount. These machines are commonly used in industries such as food, pharmaceuticals, chemicals, and cosmetics where precise filling is crucial.
- Grains, Nuts, Snacks, Namkeens, Spices , Powders, Pills, Capsules, Granular and powdered substances, Chocolates, Pet food, animal feed, etc.
- Food Industry: Used for filling products like grains, nuts, spices, and powders into containers.
- Pharmaceuticals: Precisely dispense medications, capsules, and tablets into bottles or packets.
- Chemicals: Ideal for filling liquid chemicals, detergents, and cleaning agents.
- Cosmetics: Used for filling creams, lotions, gels, and other beauty products into containers.
- Precision: Ensures accurate filling to the desired weight, reducing product wastage.
- Efficiency: Speeds up the filling process, increasing productivity.
- Versatility: Can handle a wide range of products, from powders to liquids.
- Automation: Can be integrated into automated production lines for seamless operation.
- Hygienic: Designed with materials suitable for cleanroom and food-grade environments.
- Load Cells: High-precision load cells with a capacity suitable for the intended products.
- Filling Nozzles: Various types of nozzles depending on the product viscosity and size of containers.
- Control Panel: Intuitive interface for setting desired weights, adjusting filling speed, and monitoring.
- Frame: Stainless steel or other durable materials for longevity and easy cleaning.
- Conveyor System: Optional conveyor belts for transporting containers in and out of the filling area.
- Hopper: Holds the product to be dispensed, with options for agitators to maintain consistency.
- Regular Calibration: Calibrate load cells according to manufacturer recommendations to ensure accuracy.
- Cleaning: Clean all parts that come in contact with the product regularly to prevent contamination.
- Lubrication: Keep moving parts lubricated to maintain smooth operation.
- Inspect Seals and Gaskets: Check and replace worn seals to prevent leaks.
- Electrical Checks: Ensure all electrical connections are secure and free from damage.
- Training: Train operators on proper use and maintenance procedures to prolong machine life.
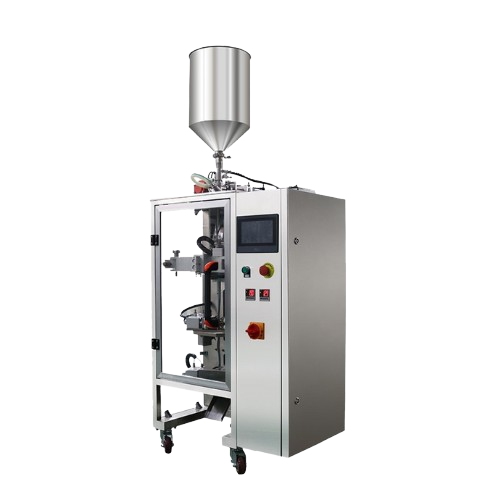
Liquid Filling Machine
A liquid filling machine is an essential piece of equipment in various industries, designed to efficiently fill containers with liquids of different viscosities. These machines are engineered to handle a wide range of liquids, from thin and free-flowing to thick and viscous substances. They are commonly used in pharmaceutical, food and beverage, cosmetics, chemical, and other industries where accurate and hygienic liquid filling is crucial.
- Shampoos, liquid detergents, Handwash, Chutneys, Sanitizers, Ketchup, Sauces, Oils, etc.
- Pharmaceutical Industry: Filling of syrups, suspensions, and other medications.
- Food and Beverage Industry: Bottling of juices, oils, sauces, and other liquids.
- Cosmetics Industry: Filling of lotions, creams, shampoos, and other beauty products.
- Chemical Industry: Filling of solvents, detergents, oils, and various chemicals.
- Household and Industrial Products: Filling of cleaners, lubricants, and other fluids.
- Precision: Ensures accurate filling to specified volumes, reducing waste and improving product consistency.
- Efficiency: Speeds up the filling process, increasing production output.
- Versatility: Can handle a wide range of container sizes and liquid viscosities.
- Hygiene: Designed for easy cleaning and sterilization, meeting strict industry regulations.
- Cost-Effective: Reduces labor costs associated with manual filling processes.
- Minimizes Contamination: Closed systems prevent outside contaminants from entering the product.
- Filling Mechanism: Different types available, such as piston fillers, gravity fillers, and overflow fillers.
- Material: Constructed with stainless steel for durability and sanitation.
- Control System: PLC (Programmable Logic Controller) for precise control of filling parameters.
- Conveyor System: Integrated with conveyors for efficient movement of containers.
- Nozzles: Various nozzle designs to suit different products and containers.
- Capacity: Available in a range of capacities to meet varying production needs.
- Power: Operates on electricity, with options for pneumatic systems in some models.
Regular maintenance is crucial for the optimal performance and longevity of a liquid filling machine:
- Cleaning: Thoroughly clean all parts that come in contact with the liquid after each use.
- Lubrication: Apply lubricants to moving parts as per manufacturer’s recommendations.
- Inspection: Regularly inspect components for wear and tear, replacing parts as needed.
- Calibration: Periodically calibrate the machine to ensure accurate filling volumes.
- Training: Train operators on proper usage, cleaning procedures, and troubleshooting.
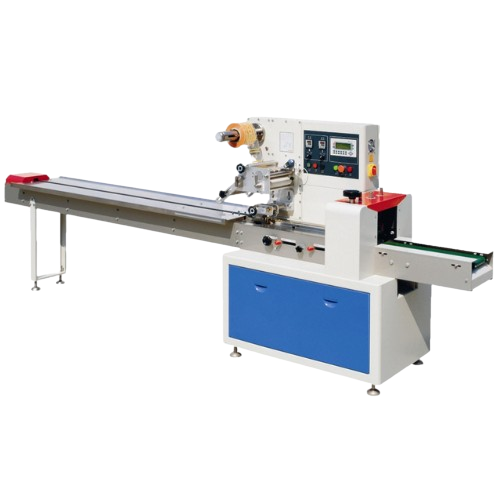
Horizontal Flow-Wrap Machine
A Horizontal Flow-wrap Machine is a versatile packaging solution designed to efficiently wrap products in a horizontal direction. This machine is commonly used in industries ranging from food and pharmaceuticals to hardware and electronics. It is capable of wrapping individual items or groups of items in a protective, sealed package, ensuring product freshness and integrity.
- Soaps, Detergent cakes, Brooms, Switches, Switch Panels, Chocolate, Chocolate Bars, Ice Cream, Cutlery Items, Dental Kits, all solid products.
- Food Industry: Used for wrapping chocolates, cookies, candies, bakery items, snacks, and more.
- Pharmaceuticals: Ideal for packaging tablets, capsules, and other small medical products.
- Hardware: Suitable for packaging bolts, screws, nails, and small tools.
- Electronics: Used to wrap cables, wires, connectors, and small electronic components.
- Consumer Goods: Can package items like soap bars, cosmetics, and small toys.
- Efficiency: Automates the packaging process, increasing productivity.
- Versatility: Can handle a wide range of products and packaging styles.
- Seal Quality: Provides airtight seals, preserving product freshness.
- Space-Saving: Compact design fits well in production lines with limited space.
- Cost-Effective: Reduces packaging costs by using less material compared to manual methods.
- Hygienic: Suitable for food and pharmaceutical industries due to its sanitary design.
- Feeding System: Products are fed into the machine either manually or via an automatic feeder.
- Film Unwinding: Rolls of packaging film are unwound and formed into a tube.
- Sealing: The product is placed in the film tube, and the machine seals the film around it.
- Cutting: The film is cut and sealed to form individual packages.
- Conveyor System: Transports the wrapped products for further processing or packaging.
Regular maintenance is crucial for the optimal performance and longevity of a Horizontal Flow-wrap Machine. Here are some maintenance tips:
- Cleaning: Regularly clean the machine to prevent build-up of debris or residue.
- Lubrication: Lubricate moving parts according to the manufacturer’s guidelines.
- Inspection: Periodically inspect belts, chains, and sealing elements for wear.
- Adjustments: Ensure proper tension of belts and chains for smooth operation.
- Training: Train operators on proper use and maintenance procedures.
- Spare Parts: Keep an inventory of commonly used spare parts for quick replacements.
- Manufacturer Guidelines: Always follow the manufacturer’s maintenance schedule and guidelines.